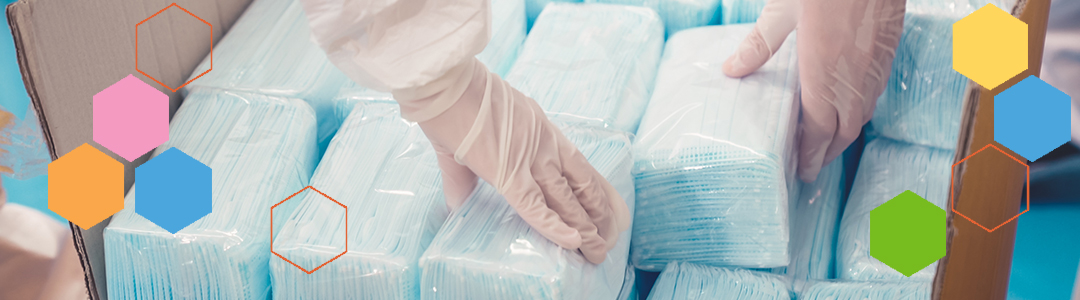
For many of us, the last time we used the word “normal” was December 2019. Since then, our facilities, teams, and supplies have been strained and stretched in every conceivable way. But during these difficult years, we came together – within our local communities and nationally – to support each other and our patients.
Let’s Talk About Resiliency
The Envi team worked with provider facilities across the U.S., engaging in conversations with Envi users about their successes – and lessons learned – along the way. Can we take these lessons of the pandemic and apply them to increase strength and agility, while inflicting less wear and tear on us all? Let’s look at what worked:
1. First, relationship matter. Take a look at what integration is possible among your existing systems. Your technology vendor partners should be able to quickly tell you what integrations have already been created and are supported, and how they can help you pass data across your systems. Disparate systems mean more data errors, more manual labor (like double keying) and less visibility.
2. Creative sourcing. When faced with supplies that were completely unavailable through traditional vendors, Envi users quickly went into punch-out capabilities, and found substitutions through online vendors like Amazon. They used Envi to research items and find alternate products they could get quickly to keep their doors open.
3. Visibility helped communities come together. Smaller organizations had a tougher time. With less purchasing leverage, it was more difficult for them to rally vendors to help them find available products. So, they worked together – among facilities and with GPOs. We heard stories from Envi users stating because they had good visibility to supplies, they could lend support by finding and sharing needed items. With sightlines throughout supply locations and accurate inventories, it was easier to participate in supporting local communities.
What’s Next?
• Scrub your item master! You may not know it, but you have a new formulary now. Decide whether the substitutions you’re using are items you want to keep in your approved formulary. Are they cheaper? Is there better availability? Do your clinicians like them? If not, cleanse them out of your item master; keep the substitutions that worked well.
• Get back to normal price management practices. Yet another crazy part of the pandemic was the lack of price sensitivity we felt. We needed supplies and we needed them now; from any vendor, at almost any price. Take a look at your new primary items and compare current prices, especially if they aren’t covered by your local or GPO contract.
• Stop hoarding! Overstocked inventory costs your facility money. It’s like cash sitting on the shelf, driving up expirations and waste. Make sure the items you bought as back-up are in your inventory counts, so you can allocate and work your way through them. Do this before reordering.
• It’s a good day for a physical count. To use up in-house inventory, you need an accurate view of what you’ve got. Envi makes physical counts easy, with the ability to see items by location. With barcode labels and a scanner, it’s done in a snap.
We’re all excited to head into this new era. The Envi team is here to help you succeed in building new processes for your best practice-based supply chain. Let’s take the lessons we’ve learned during the pandemic and use them in ways that deliver the greatest impact for our organizations and patients.