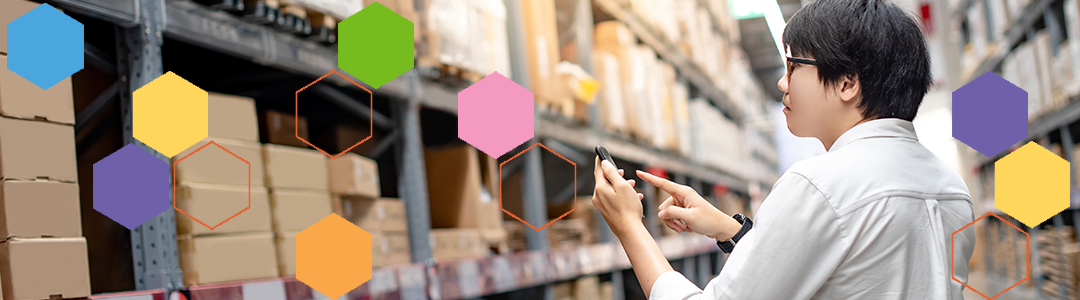
Whether your focus is fiscal, clinical, supply chain, or you zigzag between, tracking perpetual inventory is always the right thing to do.
“Ugh,” you groan. “It’s a pain.”
But there are ways to make it less painful and it really is worth it. Here’s why:
Some of your most significant savings are achieved by improving inventory management. This is a place where true hard dollar savings exist, and you’ll capture them by building visibility to inventory, and getting a better handle on management, throughout your organization.
Where the Savings Are.
Every dollar spent on supplies and devices not needed by your organization ties up cash and runs the risk of loss through damage, disappearance or expiration. Instead, create inventory management processes that help you:
- Make replenishment easier and more accurate
- Improve financial performance through increased cash flow
- Understand profitability by business line or department
- Reduce overstocking, overspending, loss and waste
- Improve planning and budgeting processes
9 Best Practices in Perpetual Inventory Management
1) Set goals to eliminate overstocking and overspending. Unturned inventory on shelves is like cash sitting in storerooms. How can you tell if you’re overordering? Look at the last 12 months of products written off due to expiration.
2) Start tracking. Track lot & serial numbers, as well as expiration dates. This will support recall management, and help you use on-hand inventory by rotating items that will expire soon to locations where they can be used.
3) Right size your inventory. Use your purchase history and patterns, with enough purchasing history (usually 12-24 months) to see usage over time and changes in seasonality. Then you can build processes that flex based on both seasonal use and overall usage patterns.
4) Increase visibility and improve management of items across all supply locations. This visibility will help you avoid overspending by moving needed items from one location to another.
5) Organize your supply areas, based on type and use of products. Consider the clinician’s needs and type of care being delivered. Make it easy for supply chain technicians and clinicians to find and replenish what’s needed. And consider limiting access to maintain better control and reduce loss.
6) Get proactive about consignment. When vendors manage consignment items and replenish automatically, the result can be that you’re spending more necessary.
7) Use inventory management processes to improve cost management: by department, business lines or physicians. When you allocate items and spend to specific departments, you can see actual costs and profitability of procedure areas.
8) Capture the products being used to improve patient billing. Tracking inventory and consumption levels helps reconcile billing activity, ensuring full billing capture based on product consumption by patient.
9) Auto-reorder the products continuously used based on consumption (not just timing). Using barcode labels and scanners are the fastest and easiest way to track and replenish supplies.
Technology is a great facilitator to improved inventory management, but you still need good processes to build upon. Use Envi best practices to help you get there. Need help? Give us a call or drop a quick note.
Learn more about Envi modules – including Inventory – that support and improve supply chain processes.