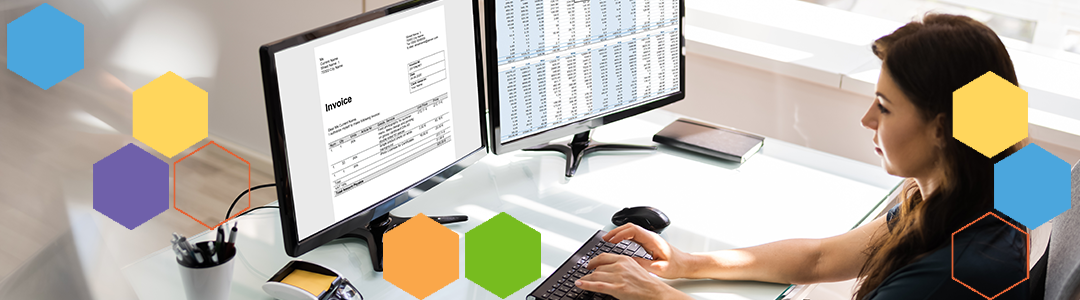
Many organizations focus on the “front end” of their supply chain as they increase automation. So they take important steps like item master cleansing, building requisitioning templates, identifying consistency in items, prices and vendors. They automate an electronic PO approval process.
But if the “back end” of your supply chain isn’t as good, you’ll miss savings, visibility and opportunities for greater accuracy and automation.
You can change your supply chain results by integrating AP with procurement.
Seven Best Practice Steps to Smarter AP
1) Create an electronic purchase order (PO) for every purchase. POs are the foundation of great AP processes and the first step toward an automated 3-way price match.
- Build PO approval on the front-end of the purchasing process to reduce time, effort and price discrepancies on the back-end. And always approve POs, not invoices.
2) Maximize EDI capabilities with your vendors. For automated 3-way matching, you’ll need electronic PO acknowledgments or ship notices (855s or 856s), or you can create for received items. You’ll also need electronic invoices (810s).
- With these 3 EDI documents, you can enable accurate 3-way matching for automated AP processing. Matching validates both price and quantity, plus you’ll eliminate manual processes and keying errors.
3) Fully leverage contract opportunities. By driving all purchasing through your approved product formulary, you can reduce prices with on-contract items.
- For your AP team, a standardized product formulary means incoming products are already identified and coded for processing.
4) Vendors still sending paper invoices? Look into conversion services that take paper documents and convert them to electronic.
- 810s make matching, payment, and archiving easier and faster, in turn reducing staff time and helping with available early payment discounts.
5) Receiving is a critical step to accurate payments. Document incoming supplies to ensure you’ve received the items about to get paid.
- While receiving may feel like an extra step it helps with both inventory management and validating accurate item counts for invoice payment.
6) Check price parity across your organization. Does every department or every location pay the same price for the same item?
- With new-found visibility, you’ll pay the right price every time an item is ordered.
7) Create a centralized location at the enterprise level for managing documentation.
- Assign a location responsible for scanning and attaching quotes, packing slips and invoices to support your internal audit processes.
Integrating AP with procurement saves time and money throughout your organization. If your current AP and purchasing systems can’t talk to each other, and your AP team is manually keying in invoices, call us. We’ll help eliminate manual steps and speed your req-to-check processes.
Envi lets you select specific modules you need. Learn more about Envi AP or other modules here.