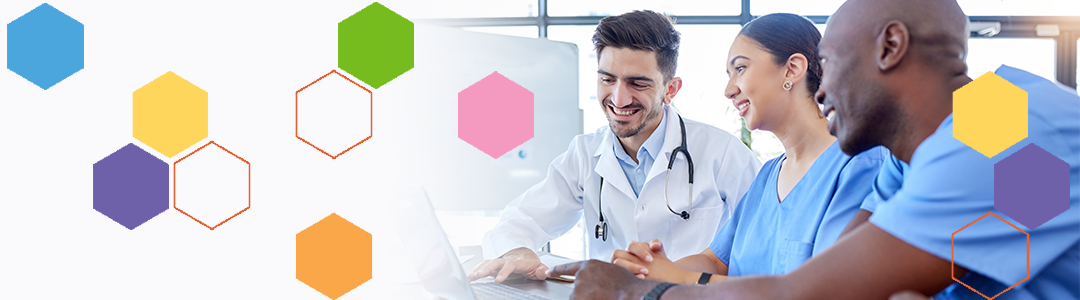
If you ask a supply chain professional at any healthcare organization what their greatest challenge is, about 95% will say data. The problems feel deeply entrenched – inconsistent application of data standards, lack of product classifications, differences in data structure and organization across disparate systems, duplicative / dirty data sets – but none of this is a surprise, is it?
To think about your next steps, let’s acknowledge the wide range of “current state” for healthcare organizations, from rapid growth through acquisition or organic expansion, to finding ways to stabilize and improve the facilities you have today. Regardless of where your organization lands, there are steps you can take to improve your data management processes.
If we think of data as the DNA of an organization, the life blood that flows through systems and processes, we can see how it touches everything we do. From facilitating the procurement of products needed to deliver care, to building and enabling the analytics needed to run at peak efficiency. Data is the master key to automation, accuracy, financial management, and even, patient outcomes.
If you’re about to set up a new procurement system, take the steps needed to get your data into better order. If you’re building a brand new, organization-wide formulary, take the time to pull data on the front end – including 12-18 months of PO history from your vendors – so you can start with a solid baseline for future procurement. Your new formulary is how you’ll drive on-contract purchasing, ensure accurate price management and on-contract spend, and even standardize procedures based on high quality / best priced products.
What if you have a formulary today but still see room for improvement? You’ll know through things like returns, off-contract spend, a high percentage of expiring products, incorrect invoices, and stock-outs. If this sounds familiar, pull together a team including finance, clinical, supply chain to identify and address data issues.
1. Look back through a year or two of spend; ensure the products most often purchased by your organization are in your item master. Focus on the most frequently purchased or highest cost items for the greatest impact.
2. Find and fix major issues, such as duplicate items or near-duplicate items from multiple vendors, items you now longer use, or items now discontinued. Removing these from your item master makes it easier to find and buy the items you need and also helps ensure back-end accuracy (invoices and reporting).
3. Ensure the products do you purchase are up-to-date, with descriptions cleansed and normalized, classified by category using UNSPSC, with unit of measure and pricing updated.
4. Consider reducing the number of vendors you use. It will simplify procurement and reporting, and may help attain better contract / tier pricing.
5. With an accurate formulary, drive your buyers to make all purchases directly from this item master, your organization’s source of truth.
To support ongoing success, determine a process for item updates, additions and deletions. Who can add to the item master? What rules will be followed? Larger organizations often have a team of people who make additions and updates to the item master. Smaller groups usually designate a single person. Ensure clear guidance is in place for anyone authorized to make changes to your single source of truth.
To ensure your supply chain is as efficient as possible, data is the difference. By building a comprehensive item master, managing contracts and spend, simplifying and centralizing wherever possible, you’re creating a more visible, accurate and automated supply chain. With this, your reporting and analytics head to the next level, making planning and forecasting with accuracy a new reality.
It really is – as they say – all about the data!