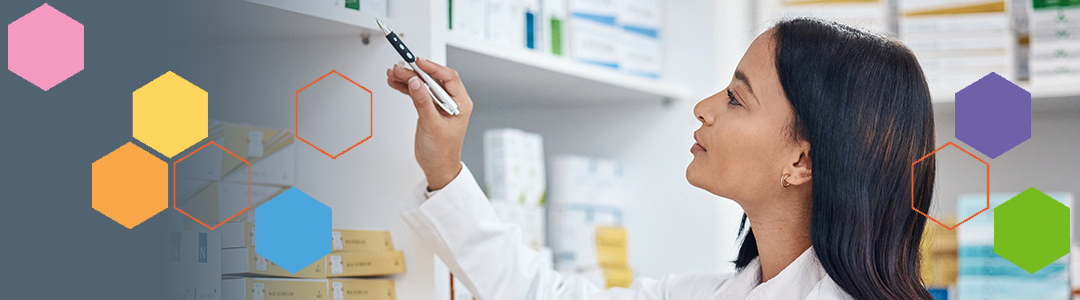
Spring. The flowers are blooming. The birds are singing. And your storage rooms are a post-Covid, unlabeled, disorganized pile of overstocked items, some of which you’re not even using. Sounds familiar? Then it’s time for Spring Cleaning! Follow these 5 tips to make your physical count gleam:
- Begin at the beginning: Your data. To ensure the accuracy of your item master, start with a Spend Review and remove items with no inventory or activity spend. Add regularly purchased free-form/punch-out items for consistency. Account for items not purchased for 18-24 months but still on hand and use Disabled Purchasing for slow-moving items. Deduplicate items and review item classifications for missing codes. These steps will lead to an accurate item master to support other areas of your business and Envi implementation.
- Price file management, validation, and updates. Before starting your inventory count in Envi, ensure that your pricing is up to date to accurately calculate the value of your on-hand inventory. Identify and update items with a $0 price, as these may have been quickly entered but never updated. Develop a plan for managing expensive consigned items and track them as part of your on-hand inventory for greater accuracy.
- Visualize the change needed in your supply areas. After cleaning up your data, organize supply areas and improve staff efficiency by creating a requirements map to identify supply needs. Organize items by type and use labels and scanners to make them easily accessible. Set goals to reduce overstocking, negotiate with overstockers, hiders and hoarders, and reduce overspending and waste.
- Use Envi tools to be ready for your count. This checklist can be an entire Best Practice article, but a quick checklist includes:
- Run the reports needed. Check count sheets and make sure the unit of measure is what you intend to count.
- Are item types updated? Verify stock items, non-stock, and consignment items are up to date.
- Leverage the “bin shelf location” field. Use a numbering system that works for you but be sure to use this field and be sure it’s accurate. It makes counting much easier!
- Be sure scanners are charged and ready to use.
- Use the 5Ps: Proper planning prevents poor performance. Planning for a count means more than just counting items. These final steps make your count a shining success:
- Process pending transactions and receipts
- Put away incoming supplies
- Identify all locations where the product is stored. Put away incoming supplies, centralizing where possible. “Walk” your shelves and make sure everything is labeled correctly and bin shelf locations are accurate.
- Update location costs. Envi has the option to update inventory locations with correct costs before counts are started. Location costs are being updated whenever you receive products through Envi, but if you’ve not run the tool recently, make sure you update location costs to make physical counts more accurate.
- Clarify the counting process with your team. Answer questions like how you’ll treat open boxes, expired products, damaged items, units of measure, etc. (Remember the 5Ps!)
Spring cleaning is important for physical count accuracy. Engage your team and make it fun by hiding prizes and using Envi. Develop a plan to use excess items and reduce inventory dollars on your balance sheet for organizational benefits.